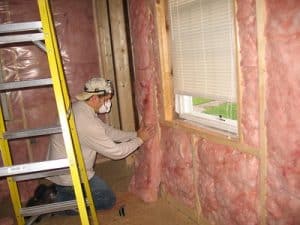
Proper manufactured home insulation shields your family from the cold of the winter and the searing heat of the summer. Whether your home properly is insulated for these seasons depends on when it was made.
Homes manufactured before the 1976 HUD have about 1 to 4 inches of very bad quality insulation – that’s if they come with any insulation at all. Back then, builders didn’t pay much attention to insulation. If you inspect your old home closely, you will locate gaps and voids throughout the structure.
Two Manufactured Home Insulation Necessitation Factors
Fortunately, the introduction of the HUD code made manufactures to start looking into finer details of better insulation. Any manufactured home produced in the last 40 or so years has quality insulation that you can upgrade easily if you feel like it. Here are some of the factors that may necessitate insulation upgrade or installation of a whole fresh layer of insulation where none existed:
1) The Need To Reduce Energy Costs
Research conducted at the Insulation Institute shows that homeowners can save about 15 percent on cooling and heating simply by adding a layer of insulation on their homes (https://bit.ly/3jq9KBH). This percentage is much higher in older poorly insulated homes.
2) The Need To Increase Comfort
Sometimes it goes beyond just saving money. A well-insulated home feels comfortable and ensures that your family stays in a cool and comfortable space during the searing sun of summer and stay warm during the winter.
What’s the R-Value?
Simply put, the R-Value is used to measure the thermal resistance of your insulation. The greater the R-value is, the better it is poised to perform. Conversely, a lower R-value means the insulation won’t be as efficient as you expected.
As you would expect, higher R-Values come with a higher price tag. Likewise, insulation with low R-Value will cost you less money.
The R-Value is a product of Temperature Difference, Area, and Time divided by Heat Loss.
R-Value = ((Temperature Difference X Area X Time)/Heat Loss)
Three variables are used to determine the R-Value
- Type of insulation
- The thickness of the insulation
- The density of the insulation
Generally, a thick material will guarantee you a greater R-Value.
But, if you attempt to compress the material to make it thin so that it can fit in certain areas, the R-Value of that material will drop significantly.
A plethora of household factors have an influence on the R-value, one of those factors is the location of the installation of the material.
Heat doesn’t flow exactly the same way through the joints, studs, and some other materials that make up your home. This means the R-value of insulation materials installed in the ceiling or the floor will be different from that of materials installed in the walls.
Another factor is the quality of the installation process or how the insulation material was installed. If you leave patches in any area of the manufactured home, the overall R-value will reduce.
An experienced contractor would advise you to buy insulation materials with an R-value between 30 and 50 for your roof and a value between 15 and 30 for the floor.
These values will still be based on the kind of HVAC system installed in your home, the climatic conditions of the region you live, and the part of the home that need insulation. This is the reason why you need to hire the most experienced contractor you can get.
What Are The Most Popularly Used Types Of Manufactured Home Insulation?
These are some of the most often used types of insulation
1) Blanket; Rolls and Batts
This is the most preferred type of insulation by many homeowners in the United States. As the name tells, it comes in the shape of rectangular pieces (batts) and cylindrical pieces (Rolls). It is often comprised of flexible fibers that can be cut into any width you wish. This feature makes them a preferable option for joint and stud spacing.
2) Foam board
Foam boards are a better alternative where rolls and bats would be too soft to function properly.
Foams tend to be more rigid. Their thermal resistance is also excellent. Foam boards are preferred for roof overs although they have lately found wide application the belly boards of manufactured homes.
3) Blown-in or Loose Fill
This type of insulation is unique in the sense that it doesn’t consist of solid slabs that must be cut into size. Instead, it consists of grains or particulate matter that can be blown or filled in any space.
It is perfect for those areas of your mobile home that are obstructed or shaped oddly.
If your home is very old, this option would work well for you because you would like to create insulation without tampering with the delicate parts of the structure.
4) Injected or sprayed foam
Foam insulation is becoming popular for tasks that involve air barriers in very tiny spaces. It is the right type of insulation for such tasks because it comes as a liquid or foam that can be squirted from a container into tiny holes.
This type of insulation isn’t best suited for floor or ceiling applications as it is for walls. However, foam insulation has come under close scrutiny over the recent years. Energy efficiency experts doubt the effectiveness of this insulation.
Numerous trends have shown that foam sprayed insulation has a much lower R-Value compared to the regularly used batt and loose-fill option. Besides, it is prone to producing messy work as it tends to ooze into the wrong areas.
What are the popularly used insulation materials?
Each type of insulation we listed above can be made from an array of insulation materials:
Fiberglass
Fiberglass is the most commonly used insulation material in manufactured homes. It is impressively resistant to rot and burn. Basically, it is pieces of glass that have been frizzled into fine fibers. The process of producing fiberglass may involve melting the glass before being rapidly blown into thin threads.
Pros
Because it is made from very soft fibers, it is highly flexible. It is both cost-effective and highly effective insulation material. Also, you don’t need specialized tools to install it – all you need is skin protection and a breathing mask.
Cons
If fiberglass ends up trapping some moisture, it will lose its effectiveness although it won’t rot.
Worse yet, fiberglass poses the same dangers as asbestos – damaged installations can cause you to breathe the tiny broken pieces of glass fibers which almost always causes damage to the lungs.
They may also provoke allergies and irritation on the skin.
The 2 types of fiberglass
Fiberglass insulation is sold in two forms: batts or rolls and a system that allows you to blow the loose fibers into remote areas.
Blown fiberglass insulation
This is the most preferred fiberglass-based insulation option for most mobile home insulation experts. That’s because batt insulation, the closet alternative, is not best suited for the tight areas often found in mobile homes – installation would be difficult.
Batt fiberglass insulation
If you are looking for a fiberglass insulation option best suited or floors joists and studs, batts would be the best option for the project. You can choose between unfaced and faced batts. Faced batts come with a paper or plastic covering on one side to ease handling and the process of installation. All need to do is to staple the paper part of the materials and start the installation process. A lot of energy efficiency experts are increasingly recommending the unfaced type.
Blown Fiberglass vs Fiberglass Rolls or Batts
Back in the 1970s when the HUD code was in pioneering years, the U.S. Dept. of Energy and the National Renewable Energy Laboratories (NREL) partnered to test an array of weatherization methods on manufactured homes located in cold climates. They found out that, if the homeowner wanted the cheapest improvement, these would be the best options:
- Blown floor insulations
- Interior storm windows
- Blown roof insulation
- Furnace turn-up
- Duct repair and air sealing
See? They mentioned blown insulation. They did tests and compared fiberglass batt and blown option and discovered that batts were prone to damages during the installation process hence lost their cost-effectiveness.
Foam boards
Homeowners who don’t prefer fiberglass tend to opt for foam boards that use plastic as their core insulation material. Foam is highly advantageous in situations where the insulation would rather be sprayed into spaces. For spaces that require rigid boards, you can choose foam boards for the task. As you can see, foam boards are made in a range of shapes, meaning they are more flexible. Also, the maker can manufacturer them from pretty any sort of plastic. Here are examples of commonly used foam boards:
- MEPS – molded expanded polystyrene
- EPS – expanded polystyrene
- XPS – extruded polystyrene
- Foamed-in-location polyurethane insulation
- Polyurethane sprayed
Pros
Foam boards are some of a tiny crop of insulation materials with thin thickness yet high insulating value. This makes them a batter option than, say, fiberglass which tends to be more voluminous. Even better off, the foam can be sprayed into awkwardly shaped areas. Foam boards are known to have excellent resistance to moisture and mold.
Cons
If you compare the cost of foam boards to that of fiberglass, the latter comes out cheaper. If you are a DIY enthusiast, you will have a hard time installing foam boards by yourself – they need specialized tools to put up.
Cellulose: recycled paper-based insulation
Cellulose insulation is perfect in areas that would have required fiberglass fibers but you would rather go with the former some reasons. Cellulose insulation options are made from recycled paper that has been ground and turned into fibers. Besides, the manufacturer may choose to use cotton, hemp, straw, or wool.
Pros
Cellulose is a better insulation option if you are into environmental conservation – the materials are environmental – friendly. Also, paper-based fibers don’t pose a serious health risk as fiberglass fibers do.
Cons
Because paper fibers disintegrate faster, you will need to replace the insulation frequently. If it absorbs water, the whole structure becomes damp and the lifespan of the insulation declines.
What Type Of Insulation Is Good For Each Part Of Your Manufactured Home?
Not just any type of insulation goes on any section of the home. You have a number of decisions to make.
- Firstly, you need to make a decision about the type of material appropriate for the project.
- Secondly, you will need to select the best way of installing your insulation.
Once you have made the above two critical decisions, you will need to hire an experienced contractor or prepare yourself if you wish to take the DIY route. Depending on the material you choose to use, you may need your contractor to have specialized tools or buy/rent your own.
The Belly and Floors
The “belly” here refers to the subfloor or the part immediately below the observable floor system.
Fiberglass rolls/batts would be the best type of insulation for the belly if you have access total access to the underneath of the floor – let’s say the floor is damaged or the belly wraps are missing.
However, you will need to make a few extra cuts on the structure fit the batts and rolls on the joists. Remember to be careful while at it because you might compromise the efficiency of the materials if they end up damaged.
Foam boards are a better alternative to fiberglass rolls/batts if you still have total access to the underbelly. Still, you will need to make a few extra cuts. Fortunately, you can choose to take the DIY route this time because foam boards don’t require specialized tools to install.
The blower option (spraying the insulation into the voids) would be a better option if you have very limited access to the underbelly.
NOTE: Floor cavities in manufactured homes tend to have belly wraps (‘blanket’ that attaches to the underneath the 2”x6” joists.
If your manufactured home came with transverse joists (joists that follows the width lane of your home), the position of your ducting could create a dropped belly that could potentially cause issues if you try to blow the insulation into the spaces. Hence, the belly should attach properly to the joists to leave smaller channels requiring less insulation.
Wing and Rim Joist
You can pump the insulation into the underbelly of your manufactured home via the wing and rim joist. But you’ll need to drill a few holes into these structures first before forcing the insulator inside. However, many contractors would advise you against this technique if the rim joists are part of the foundation.
Walls and Sidings
Manufactured homes made in prior to 1976 have thin sidewalls which also means poor insulation. Insulation rolls and batts are appropriate for such walls because they are easily cut and trimmed into the correct size to fit within such walls through a technique called stuffing and without much interference.
If you are remodeling your home and you will be removing all ceilings and walls, this is still the best type of insulation. You can choose to blow material into the spaces or use the Drill-and-Plug technique.
Manufactured Home Insulation Tips – 3 More Areas of Concern
1) Roof
The roof is another primary structure through which your manufactured home can lose heat. you can install roof insulation using one of the following common methods.
- Drill and tube-blow from the inside
- Drill and tube-blow from the top or
- Roll the roof back and blow into the open cavity
Roof cap insulation is also a common alternative to the three methods above.
The roof cap method also comes with additional benefits. For instance, it can also serve as a roof sealant for leaky roofing.
While roof insulation is not always a piece of cake, you can reduce your heating bills by up to 15%.
More often than not roof insulation goes hand in hand with ceiling insulation.
2) Windows\Doors
Windows and doors are also a major source of heat loss in homes. To get more from your home insulation efforts, insulating these parts of your home could bring more benefit. There’s no point in insulating all the other areas, only for the extra heat to escape through the windows.
This is often referred to as weatherstripping or caulking. You can simply improve your home’s energy efficiency by adding some window coverings made from removable plastic.
Foam tapes are also common in window insulation.
Most of these coverings are disposable and can be removed during the hot season. The alternative is to invest in energy-efficient windows, most of which are also storm proof.
3) Air Ducts
The air ducts are a highly important system when it comes to manufactured home heating, ventilation, and air conditioning. However, they are also prone to causing heat loss during the cold season.
Air duct insulation can reduce your home’s heating costs by a significant margin. In most cases, however, this is performed by highly trained and experienced HVAC experts.
It is also advisable to air seal any openings near and around plumbing fixtures. Also, consider having your HVAC system checked for leaks.
Loose joints and ducts around these units can always be sealed using metal duct tape.
How Do You Prepare For The Insulation Project?
Before even embarking on the insulation project, there are a few things you need to get right:
Check local codes
Checking what your local codes are saying regarding the remodeling or home update projects. This is especially important if you choose to employ DIY techniques for installation. Local codes take into account the unique issues facing the homes in the locality. Be sure to do your research and find out what they say regarding the installation of insulation.
The 4.5” leftovers
How many 4.5” leftovers will you produce?
Where will you take them?
For every 48” wide board you cut to obtain 3 pieces, a 4.5” leftover will be produced.
The leftovers can be put to various uses, but how will you use them, specifically in your case? The larger the project, the more of these pieces you will produce.
Ground moisture
If you are planning to insulate the floor, it would be useless to proceed with the project if the floor is prone to moisture penetration. Check the condition of the floor before starting. If the moisture barrier is wanting, consider installing it first before anything. In some cases, you will need to combine the moisture barrier with the vapor barrier – seek the advice of your contractor.
Conclusion
The two reasons why you may consider a layer of insulation on your manufactured home is to reduce your expenditure on energy consumption and/or make the living space comfortable.
Whether you choose fiberglass rolls/batts or foam boats, you will need to check what your local codes say about home remodeling and upgrades. It is also important to put into consideration how you will get rid of the leftovers as well as whether your floor is protected from the ground moisture or vapor.